Advanced Welding WPS: Tailoring Requirements for Complicated Tasks
Advanced Welding WPS: Tailoring Requirements for Complicated Tasks
Blog Article
Understanding Welding WPS Criteria: Ideal Practices and Techniques for High Quality Welds
In the realm of welding, understanding Welding Treatment Spec (WPS) criteria is a vital element that directly affects the top quality and integrity of welds. Abiding by these requirements makes certain uniformity and dependability in welding results. Nevertheless, accomplishing quality in welds goes beyond simply understanding the criteria; it involves executing ideal practices and techniques that raise the craft to a level of precision and skill that establishes apart the average from the outstanding. As we browse via the intricacies of welding WPS criteria, discovering key understandings and strategies for accomplishing top-tier welds will be extremely important for welders seeking to master their craft and produce welds that stand the examination of time.
Recognizing Welding WPS Criteria
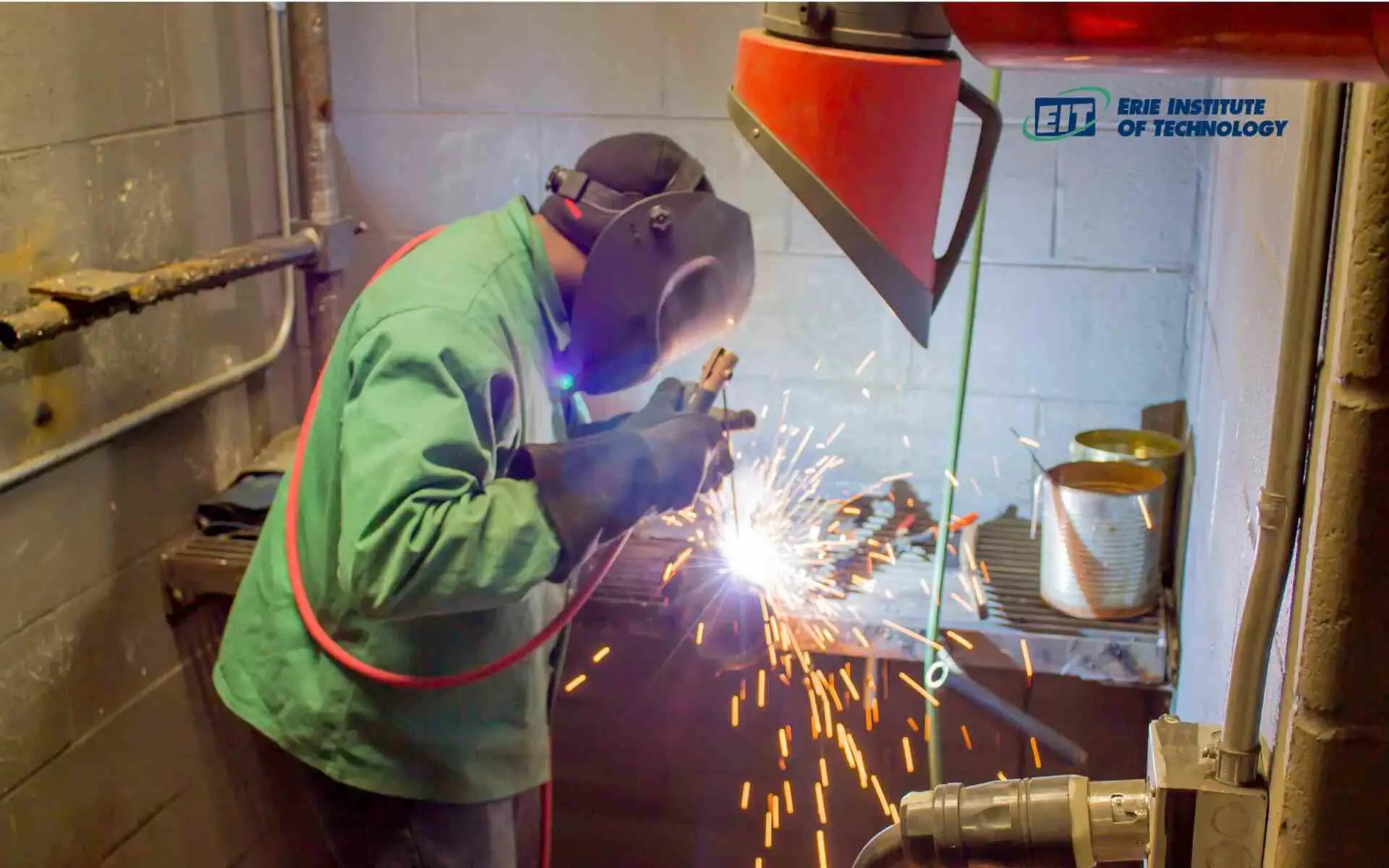
Examiners rely on WPS documentation to validate that welding procedures are being adhered to properly and that the resulting welds are of high top quality. Designers utilize WPS criteria to create welding treatments that make sure the resilience and reliability of bonded structures.


Important Devices for Quality Welds
Understanding welding WPS requirements is important for welders to properly use the essential devices required for generating quality welds. Among one of the most important tools for top quality welds is a welding equipment. The kind of welding maker needed depends on the welding process being used, such as MIG, TIG, or stick welding. Welding helmets are likewise essential to shield the welder's eyes and face from sparks, heat, and UV radiation. Furthermore, welding gloves constructed from heat-resistant and sturdy materials protect the hands from injuries and burns. Magnets and clamps assist hold the workpieces together firmly during the welding procedure, making sure exact and precise welds. Cable brushes and damaging hammers are important for cleaning up the weld joint prior to and after welding to eliminate any type of pollutants that could influence the high quality of the weld. additional hints Last but not least, a determining tape and angle mill are useful devices for making sure correct positioning and preparing the workpieces for welding.
Key Methods for Welding Success
To accomplish welding success, one should master the vital strategies necessary for generating premium welds. Maintaining a stable hand and a steady welding setting throughout the procedure is vital to achieving precision and consistency in the welds. By understanding these key methods, welders can elevate the top quality of their work and achieve welding success.
Ensuring Conformity With WPS Standards
In addition, welders should undergo training to acquaint themselves with the WPS standards appropriate to their job. Routine audits and inspections need to be carried out to validate that welding tasks align with the suggested WPS guidelines. Additionally, preserving in-depth documents of welding specifications, devices calibration, and evaluation outcomes is essential for demonstrating compliance with WPS criteria - welding WPS. By faithfully adhering to WPS criteria, welders can ensure that their work meets the needed high quality levels and adds to the total success check my reference of the welding job.
Troubleshooting Common Welding Issues
When confronted with common welding issues, determining the origin is important for reliable troubleshooting. One widespread issue is the presence of porosity in welds, typically triggered by impurities such as moisture, rust, or oil. To address this, making sure appropriate cleansing of the base metal before welding and making use of the proper securing gas can dramatically lower porosity. Another issue often experienced is lack of combination, where the weld stops working to correctly bond with the base product. This can originate from inadequate warmth input or improper welding method. Readjusting criteria such as voltage, wire feed rate, or take a trip rate can help enhance fusion. Furthermore, distortion, cracking, and spatter prevail welding difficulties that can be minimized through correct joint preparation, regular heat control, and selecting the proper welding Get More Information consumables. By thoroughly recognizing these common welding concerns and their source, welders can efficiently repair problems and achieve premium welds.
Verdict
To conclude, understanding welding WPS criteria calls for a comprehensive understanding of the standards, using necessary devices, and applying crucial strategies for successful welds. Making sure conformity with WPS requirements is crucial for producing high quality welds and staying clear of common welding problems. By following best strategies and practices, welders can achieve regular and dependable lead to their welding jobs.
In the realm of welding, understanding Welding Treatment Specification (WPS) standards is a vital element that directly influences the quality and stability of welds.When delving into the world of welding methods, a crucial element to comprehend is the importance and complexities of Welding Treatment Spec (WPS) criteria. WPS requirements offer an in-depth guideline for welding operations, making certain uniformity, top quality, and safety and security in the welding process. The kind of welding equipment needed depends on the welding process being utilized, such as MIG, TIG, or stick welding.Achieving welding success with the proficiency of essential techniques necessitates a thorough understanding and adherence to Welding Procedure Spec (WPS) standards.
Report this page